Here is a typical CCFL Backlight replacement. All assemblies will be slightly different but very similar. Use this as a general guide or to help you determine if changing out a CCFL bulb is for you. If not we offer a mail-in service as well.
This is a dual lamp assembly but the same process applies wether you are soldering a single, dual or triple lamp assembly.
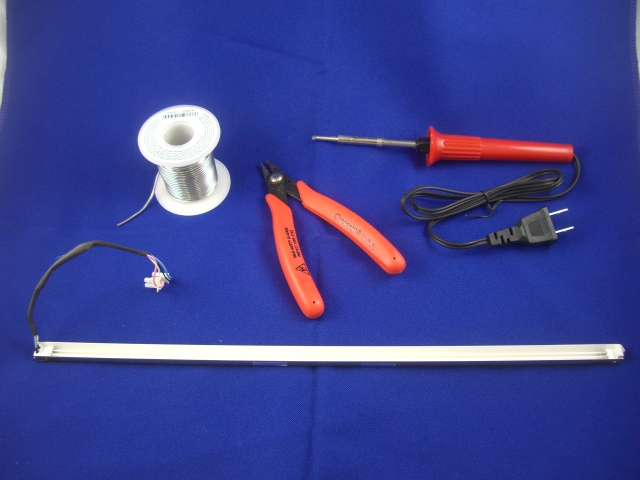 |
Here is a typical dual lamp assembly that you might find in
many different LCD monitors along with the tools necessary to complete the
job, soldering iron, solder and small wire snips. In place of the
small wire snips you can use a sharp pair of scissors. You may also wish to
have some wire strippers on hand if you have them available. A very small
pair of needle nose pliers can also be handy but are not necessary. |
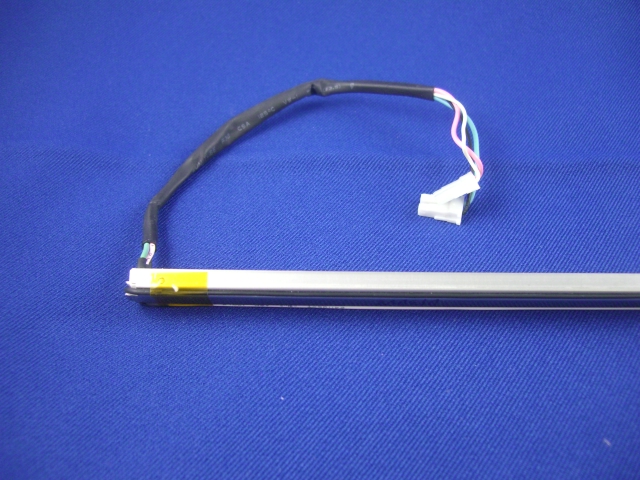 |
Most assemblies will include a small section or two of
Kapton Tape used to hold the wires in place. This is a specialized tape
designed to minimize capacitive loading or voltage leakage. It is available
in our accessories section, however if carefully removed it can be reused.
|
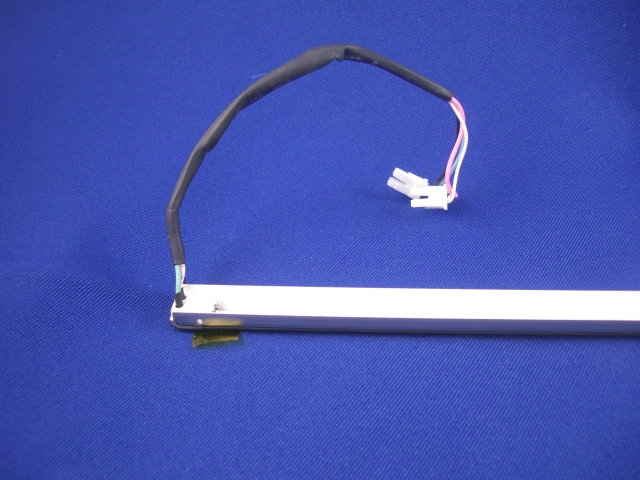 |
Remove tape so that you can free up the wires that run
along the bottom of the assembly. |
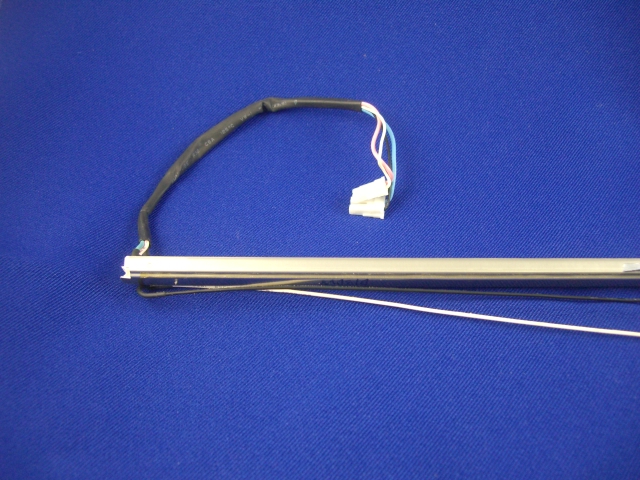 |
Pull the wires free of the assembly. |
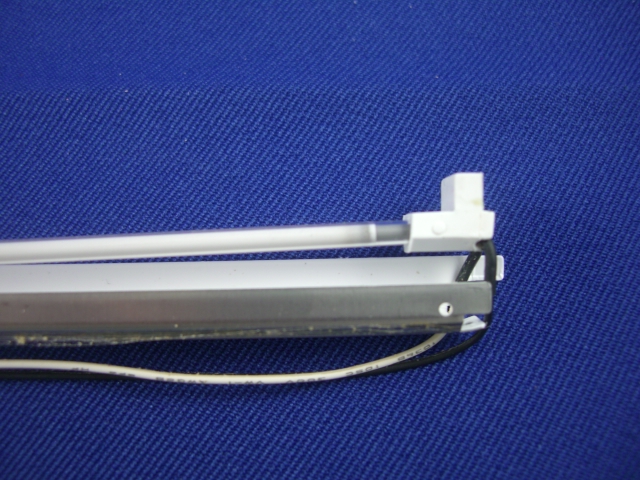 |
Carefully remove the lamp assembly from the metal or
plastic channel . |
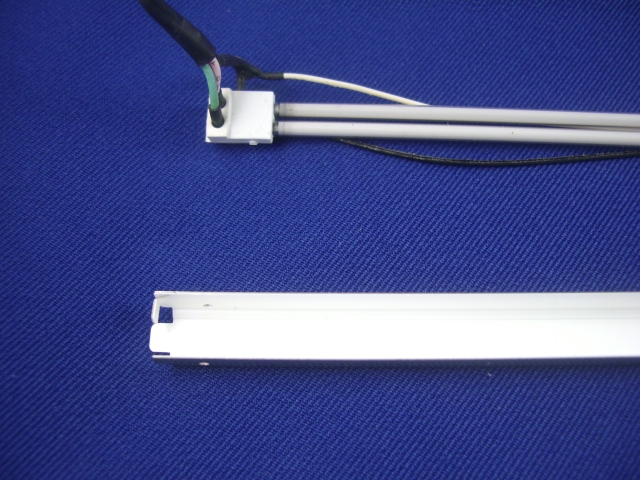 |
Set channel aside for later reassembly. |
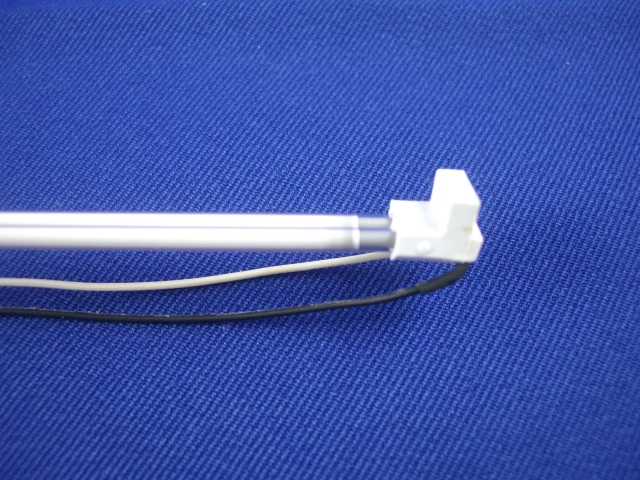 |
Next you will remove the silicon end caps. Often times they
can be difficult to remove as the heat of the lamp has caused them to stick
to the glass. Take your time and and slowly separate the glass from
the end cap being careful not to damage the silicon end caps to badly. Small
tears and cracks are common and usually will cause no problem in the
reassembly. If your end caps are damaged beyond repair you will need to
check our accessories section for a compatible end cap. *TIP*
You can also use a small amount of silicon caulking to repair torn caps. The
key is to make sure that no metal is exposed. |
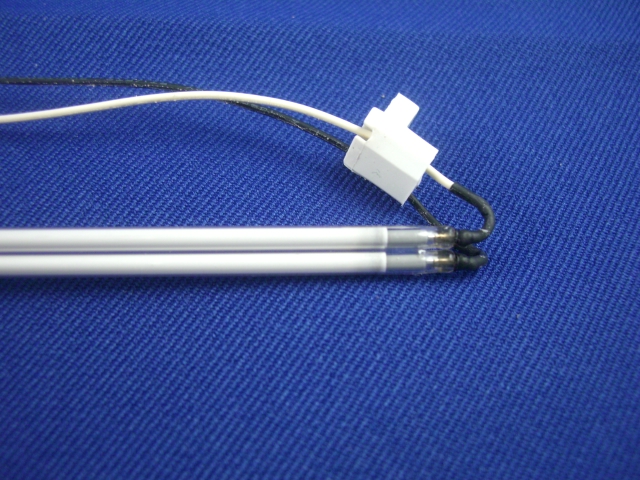 |
Slide the caps up the wire. Do not remove the cap as it
will be to easy to lose your orientation and will make reassembly very
difficult. |
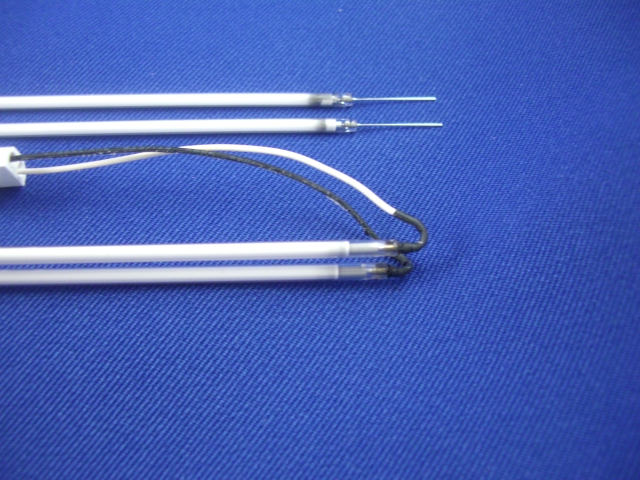 |
With caps removed, double check that your lamps are of the
correct length. Lamps should be exactly the same size as the originals or
even up to 5mm shorter but never longer than the original. Also note
that the long electrode will be trimmed down to size in a later step. |
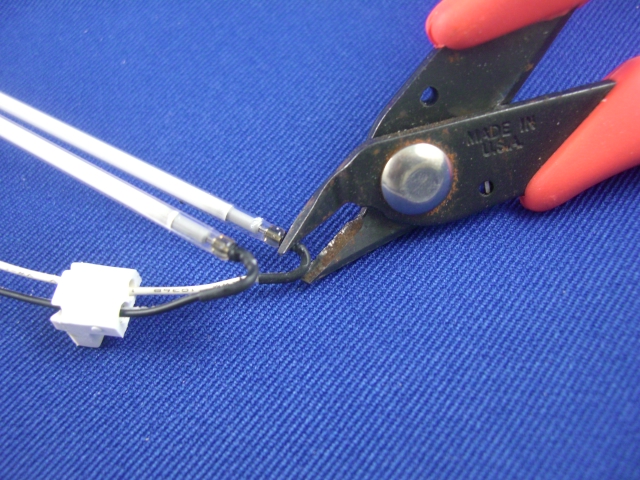 |
Using the small snips or scissors cut the wire away from
the old lamps. You will want to make sure to trim as close to the lamp as
possible so that your wires are not to short for reassembly. Make sure to
observe the condition of the wire. If the wire shows burn marks or cracking
or peeling insulation you will definitely want to replace the wire. You can
find replacements in the accessories section. |
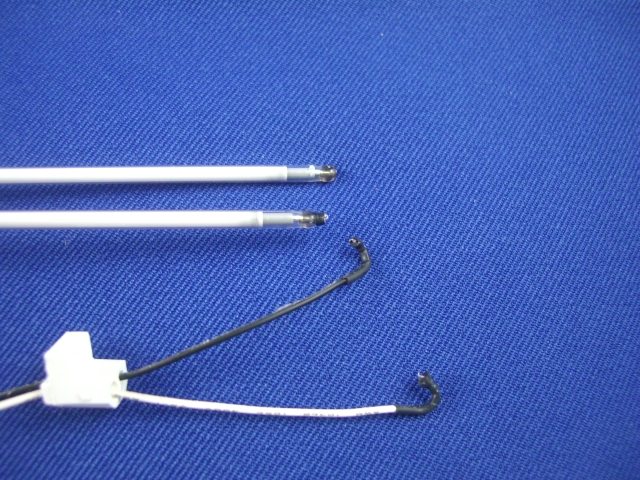 |
Wires removed and ready to be prepped for new lamps. |
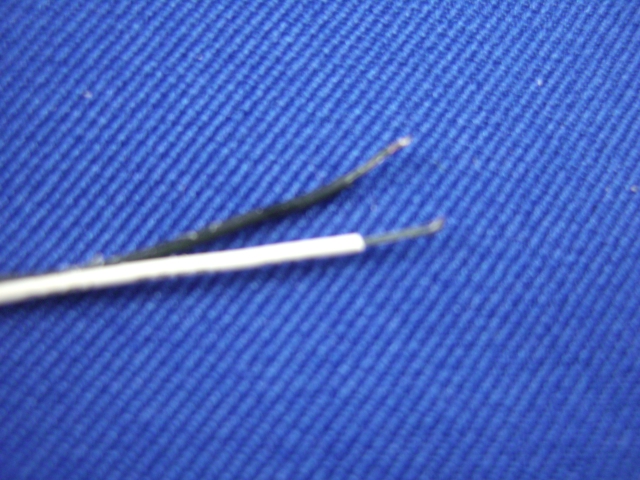 |
You will now want to strip a small section of the wire
sheathing approx. 4-5mm from the end of the wires. The use of wire strippers
is ideal here but you can also use the small snips if you are careful not to
cut the braided wire inside. |
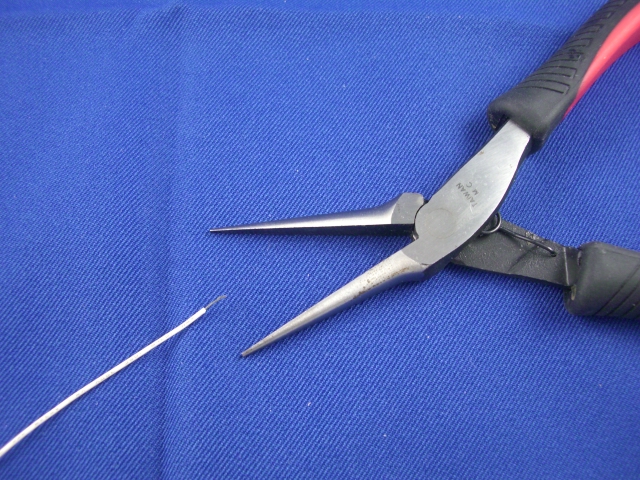 |
The next step will be to make a mall loop on the end
of the wire for easy soldering and assembly. |
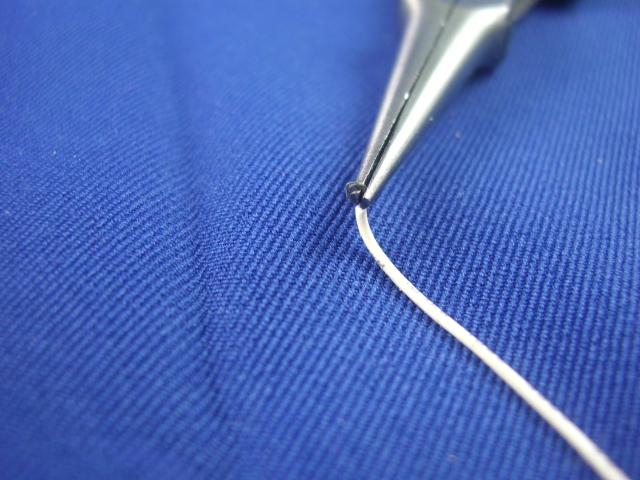 |
Using the small needle nose pliers you want to roll a small
loop in the end of the wire. You can also use a small finish nail, thumb
tack or even a paper clip to wrap the wire around as long as you can make a
small loop. |
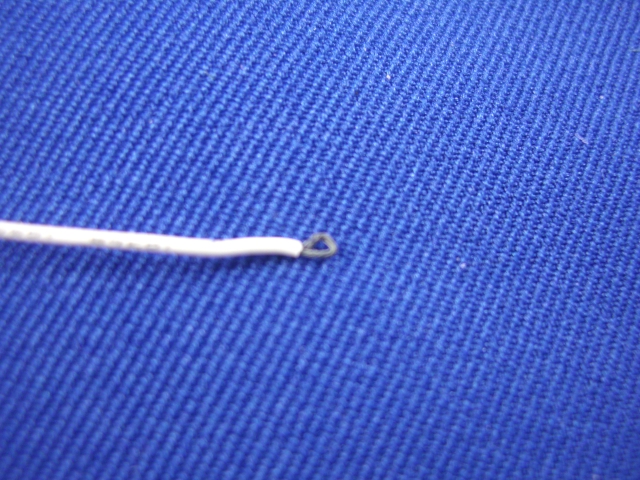 |
Your small loop should look something like this. Taking
your time to make everything right will make things much easier when it
comes to soldering. |
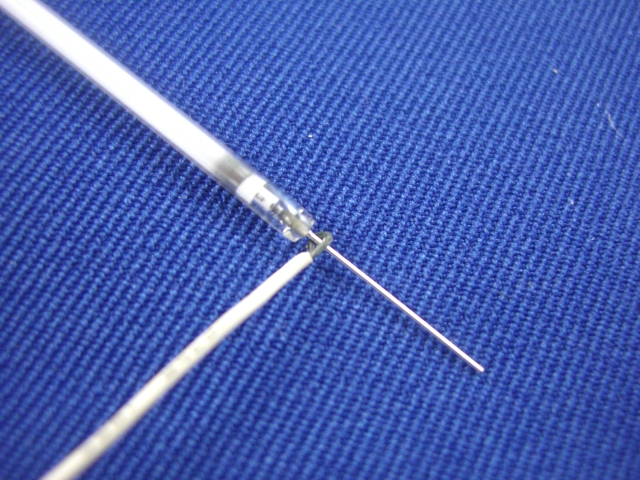 |
After you have looped the ends of the wire you will want to
slide it up the electrode right next to the glass. You are now ready to
solder. |
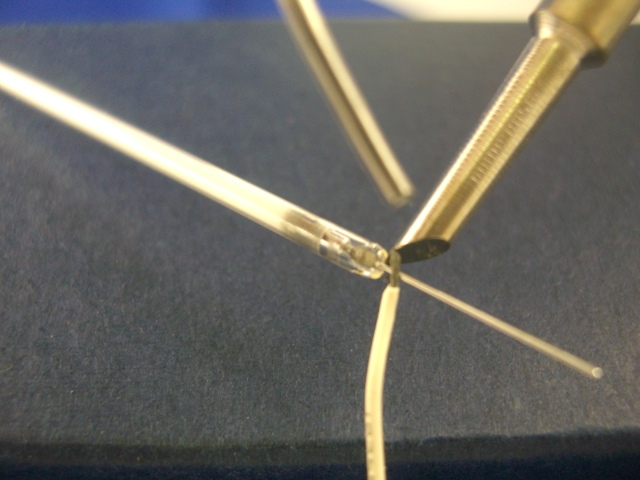 |
Soldering is actually quite easy. Make sure the tip of your
soldering iron is clean of old solder residue to allow for a clean solder
joint. Try to heat both the electrode and the wire for a few seconds before
applying the solder. If you use a flux core solder like that offered on our
accessories page you will simply need to touch the solder to the hot tip
which is in contact with the wire and electrode and the solder should pool
into a small joint. as pictured below. |
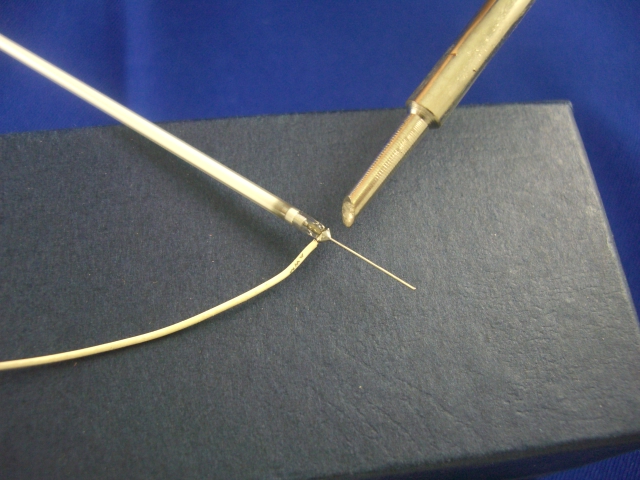 |
This is what a good solder joint should look like. Not too
much solder. Pay attention when you disassemble your one and try to
replicate exactly as the original. Most importantly make sure that your wire
makes good contact and is not loose. For your reference only, Below is
what a solder joint should not look like. You will need to remove the solder
by reheating it and start over. |
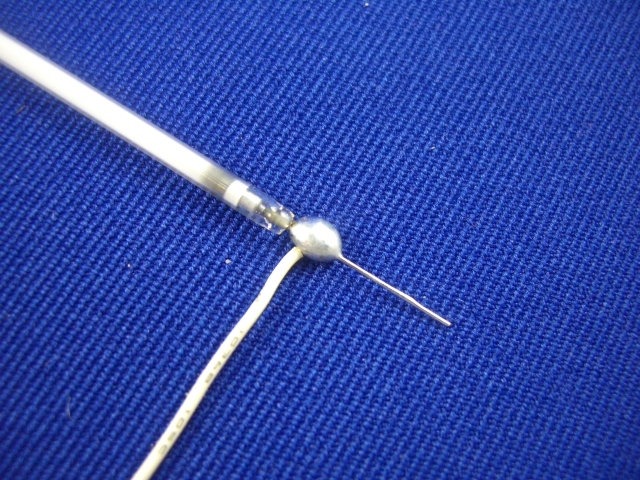 |
If your solder joint looks like this you will need to start
over or practice on a scrap piece of wire. You do not need very much solder
for good contact. |
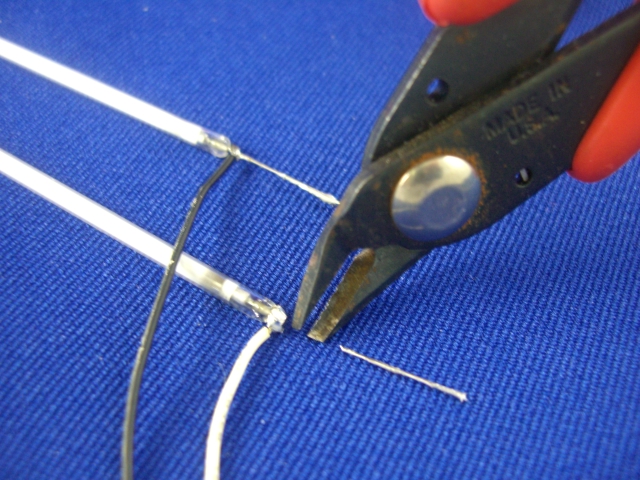 |
With your solder joints completed you will now want to trim
off the excess electrode. Using the snips or scissors trim the wire right up
to the solder joint. You can also use these to trim off excess solder if
your joint is a little too large. |
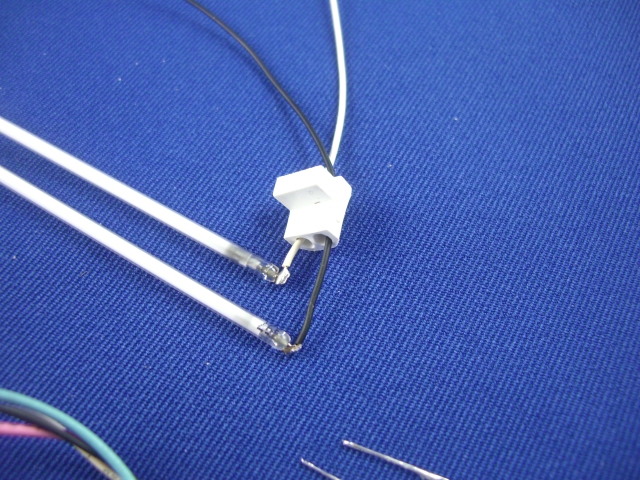 |
You are now ready for reassembly. |
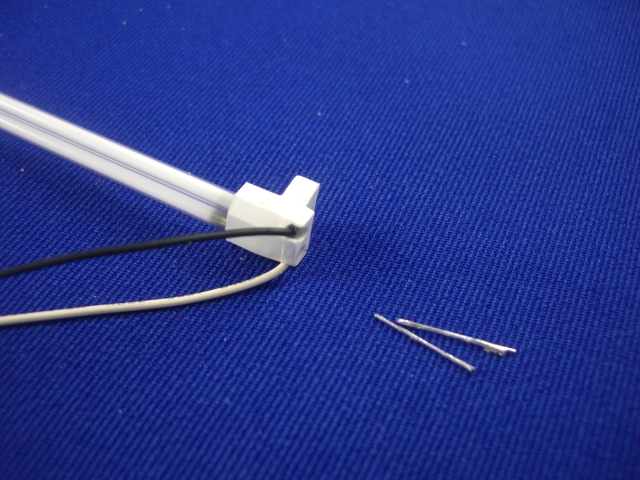 |
Slide the silicon cap back over the lamps as it originally
was. At this point you may wish to test the lamps to make sure that the
solder joints are good and that everything is working. You don't want to
completely reassemble your LCD only to find that one of your wires was loose
and your display does not light up. Be careful not to touch any part of the
assembly when testing as it is a high voltage device and can shock you. |
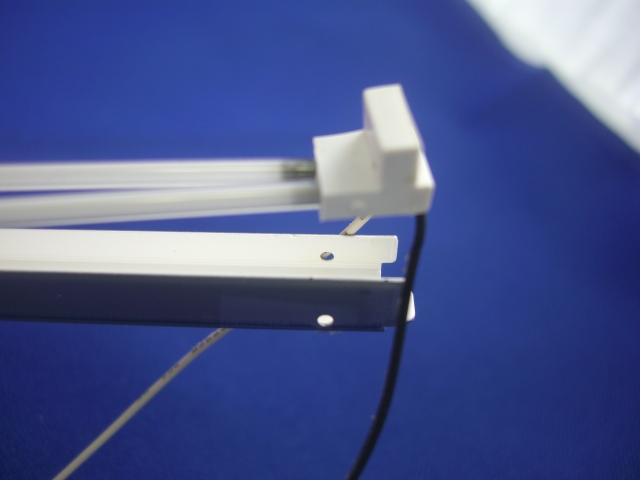 |
You can now re insert the assembly into the channel, simply
reversing the steps from the beginning. |
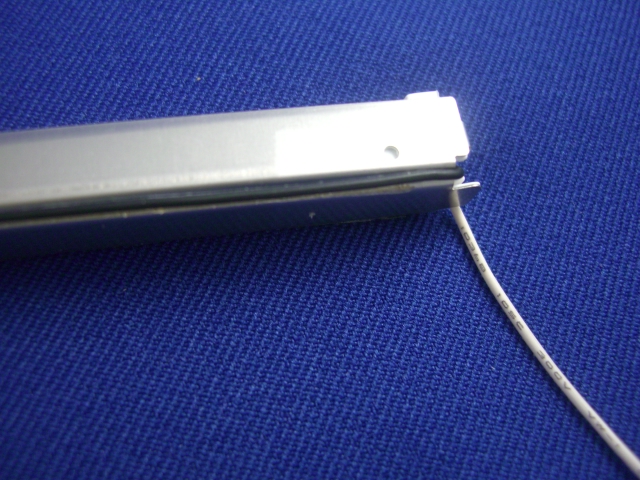 |
You will want to run the wires back along the grooves in
the channel just as they were previously. |
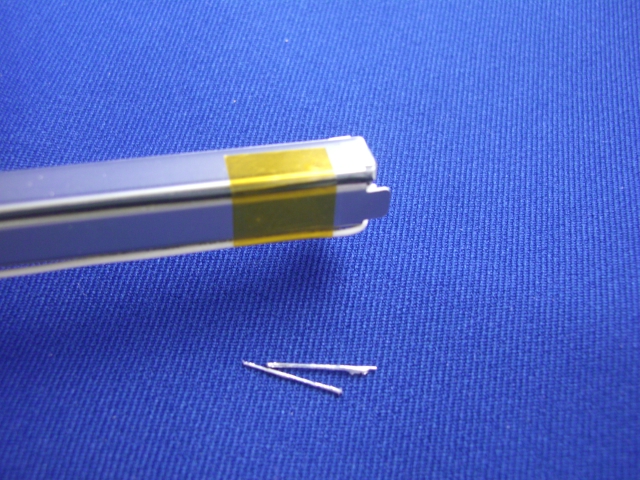 |
Make sure to replace the tape to hold the wires in place
and you are ready to reassemble your LCD. |
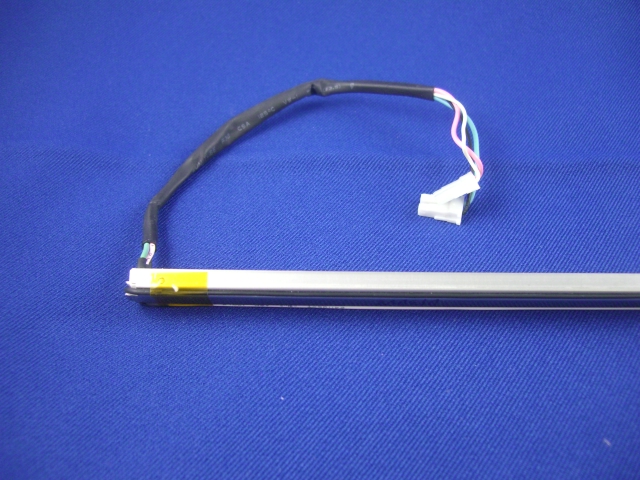 |
A job well done. |